
For the majority of applications, gray iron is used in its as-cast condition, thus simplifying production.
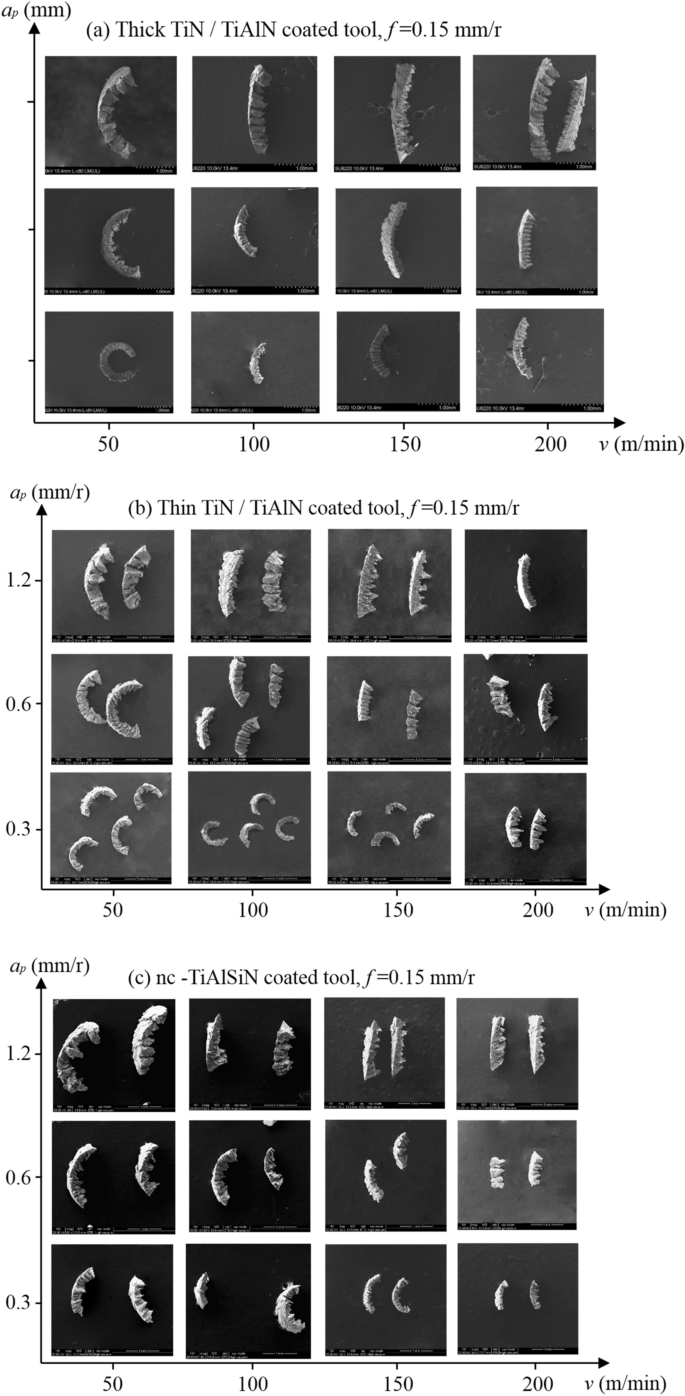
As a result of a peculiarity during final stages of solidification, it has very low and, in some cases, no liquid to solid shrinkage so that sound castings are readily obtainable. It has the lowest pouring temperature of the ferrous metals, which is reflected in its high fluidity and its ability to be cast into intricate shapes. Gray iron is one of the most easily cast of all metals in the foundry. It is the purpose of this paper to bring to your attention the characteristics of gray iron which make the material so useful. Gray iron castings are readily available in nearly all industrial areas and can be produced in foundries representing comparatively modest investments. It has a number of desirable characteristics not possessed by any other metal and yet is among the cheapest of ferrous materials available to the engineer. There are several reasons for its popularity and widespread use. For 1967, production of gray iron castings was over 14 million tons, or about two and one-half times the volume of all other types of castings combined. Next to wrought steel, gray iron is the most widely used metallic material for engineering purposes. In spite of competition from newer materials and their energetic promotion, gray iron is still used for those applications where its properties have proved it to be the most suitable material available. Gray iron is one of the oldest cast ferrous materials. Shaw, Executive Director, Iron Casting Research Institute We hope this clarification will be informative and useful to both casting producers and users. This effect is also influenced by other metallurgical conditions peculiar to each base iron so that the optimum range needs to be determined for each particular melting operation. Running toward the low end of the range would normally maintain higher hardness and tensile strength while running toward the high end would decrease both. For example, for an iron with 0.10% Sulfur, the optimum range for Manganese would be 0.47% to 0.67%. However, low levels too close to this 1.7 “balanced ratio” tend to promote high and more erratic hardness and/or carbides.Ĭonsequently, for most applications the optimum operating level for manganese appears to be about (1.7 x % Sulfur), + 0.3% to 0.5%.
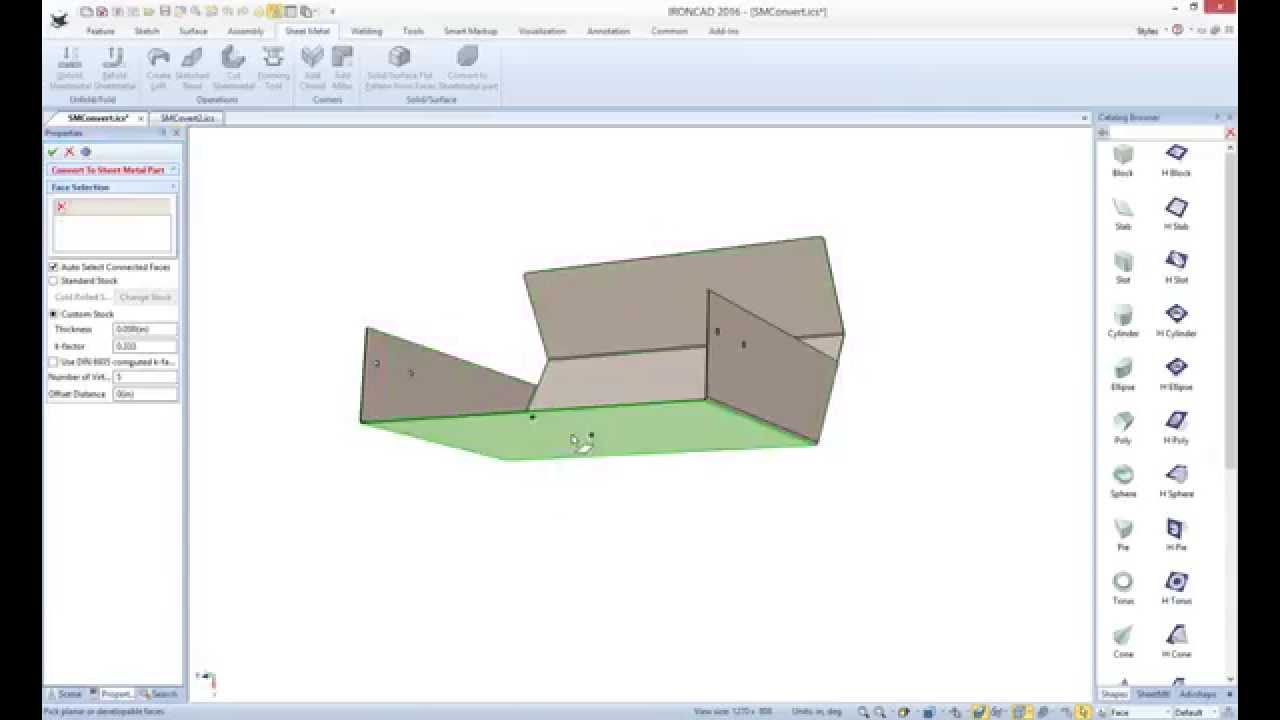
In contrast to the traditional view of these elemental effects noted herein, work in the 1980’s confirms that in many cases manganese levels beyond that amount combined with sulfur (about 1.7 times the sulfur level) tend to reduce strength and hardness via promotion of more ferrite. This is the matter of manganese and sulfur effects. While this brief technical paper, originally presented in 1969, is still one of the best summaries of gray iron metallurgy and properties, we call your attention to one item on which recent research and foundry experience has shed more light. To: All readers of report on Gray Iron by D.E Krause KEY WORDS: gray iron castings, casting design, foundry methods, ductile iron castings, malleable iron castings, metals, tests, evaluation
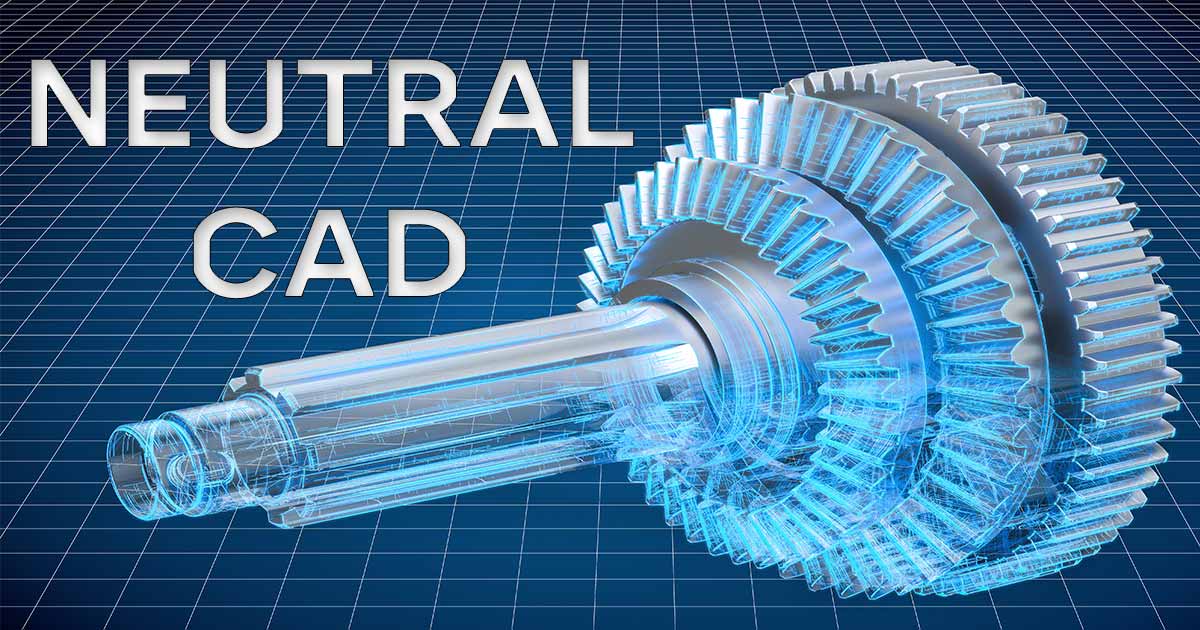
Although the relationship between Brinell hardness and tensile strength for gray iron is not constant, data are shown which will allow use of the Brinell hardness test to estimate the minimum tensile strength of the iron in a casting. An unnecessary increase in strength and hardness may increase the cost of the casting as well as increase the cost of machining through lower machining rates. By subsequent heat treatment, the hardness can be increased to H g should be carefully reviewed before specifying a higher strength and hardness grade of iron. By suitable adjustment in composition and selection of casting method, tensile strength can be varied from less than 20,000 psi to over 60,000 psi and hardness from 100 to 300 BHN in the as-cast condition. The low degree or absence of shrinkage and high fluidity provide maximum freedom of design for the engineer. The high carbon content is responsible for ease of melting and casting in the foundry and for ease of machining in subsequent manufacturing. 3-28.ĪBSTRACT: Gray iron is the most versatile of all foundry metals. E., “Gray Iron-A Unique Engineering Material” Gray, Ductile, and Malleable Iron Castings-Current Capabilities, ASTM STP 455, American Society for Testing and Materials, Philadelphia, 1969, pp.
